According to Stephen Hodgson, chief executive of the Property Care Association, retrofit insulation changes the way a building works in ways not always apparent.
While this does not mean that buildings shouldn’t be insulated, he says there needs to be a greater awareness of the implications of what might seem like innocuous improvements to the building fabric & insulation projects.
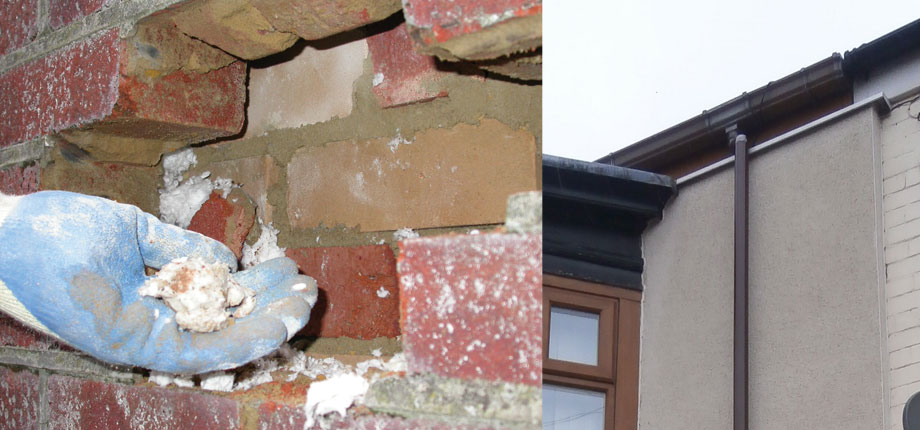
Retrofit Insulation and external walls
Materials applied to existing structures to improve thermal performance fall into three groups - Internal Wall Insulation (IWI) Cavity Wall Insulation (CWI) and External Wall Insulation (EWI).
All these systems are designed to reduce the rate an occupied space loses energy in the form of heat by conduction through thermally inefficient solid materials (bricks and mortar) and by convection where unwanted air gaps allow heat to dissipate, driven by vapour pressure differential or convection currents.
From a PCA perspective, the two areas where we can share greatest insight are Cavity Wall Insulation and External Wall Insulation, and these are addressed below.
Cavity Wall Insulation projects
If done correctly CWI is effective and cost-effective. Well-designed, appropriately installed CWI poses little risk of exacerbating damp problems in well-maintained homes.
The cavity wall is a tremendously robust and resilient form of construction. Internal damp where CWI is a factor is almost always the result of inappropriate, ill-considered or defective installation. The fact that insulation was present when the water got into the cavity can also be very significant. When cavities are filled there is material continuity between the prevailing weather-resisting external leaf and the internal wall finishes. CWI effectively changes a cavity wall to something that has more in common with a solid wall.
In well-constructed cavity wall buildings, even in exposed locations, rainwater penetration is uncommon. Where it does occur, the cause is usually wind-driven rain, linked with other construction defects such as missing seals, bad detailing or solid objects, directing running water across the cavity or providing a vector for its transfer as capillary moisture.
CWI seldom reduces the effects of wind-driven rain. More commonly, its presence is a vector to transfer. Moreover, the insulation can encourage the retention of moisture and impact on drying. We are recording that even minor defects to the external weatherproof envelope of the building can become significant and lead to dampness inside the building where the cavities are filled with insulation.
Cavity walls filled with insulation are different from those with clear cavities. They perform differently and provide new challenges to those who own, inspect and repair them.
External Wall Insulation
With little disturbance inside the building, walls can be refreshed using high performance insulators that provide very good thermal performance and can improve the look of almost any building. When EWI is delivered properly to well-maintained and defect-free walls, all indications are that the thermal performance gains will be good and the risk of defects leading to damp problems are very low.
Pre-application, any defects in the external fabric of the building should be addressed and rectified, occupier assessment noted and any improvements to the ventilation systems made. Mounted pipes and electrical services should be considered, for relocation in front of the new insulation. Roof profiles at eves and verges should be extended to allow the insulation to be positioned correctly and guttering to be fixed appropriately.
Architectural features need consideration, and interfaces with neighbouring buildings, extensions, garden walls and fences, as well as utility meters, TV and telephone terminals, satellite dishes and any other incidentals.
While EWI is growing in popularity, we do see that these considerations can be overlooked or ignored.
In almost every installation we have visited, design defects or the execution of EWI has resulted in what can only be described as potentially significant defects.
Leaving panels un-insulated and failing to deliver continuity in a system is incorrect and undesirable and can lead to problems associated with internal mould. Most troubling is the long-term implications of the use of cut-outs and cover strips to allow insulation to be applied around obstructions, architectural features, pipes and services.
EWI is usually fixed to underlying walls using mechanical fixings or adhesives. The insulation usually exceeds 100mm in thickness, protected by high-performance waterproof or water-resisting coatings. The result should be a high-performance monolithic finish, that is expected to resist water penetration for decades.
Attention needs to be paid to eliminate any feature that could result in water getting behind these impervious coatings. We’ve seen properties with soil pipes, gas meter boxes, boiler flues, soil stacks and street signs worked around. Worse still is the failure to extend roof lines that results in the insulation sticking-out beyond the protection of the roof covering. The use of uPVC cover strips to seal the insulation at high level is common but they are often held in place with silicone adhesives – which is also cause for concern.
There’s the effect of water getting behind high-performance weatherproof coatings and insulation, especially where the underlying walls are of solid construction. As coatings will retard drying, it is safe to assume fungal decay in structural timbers and dampness in internal finishes will result.
Although water penetration issues are relatively easy to remedy in a building without EWI bolted to its exterior, the complications of delivering a solution where the removal of an EWI system may be fundamental to the remediation package are significant.
Ventilation
Modern buildings are increasingly reliant on mechanical air management to provide good air quality. It is also a fact that properly installed retrofit insulation reduces uncontrolled air leakage. It goes without saying that good retrofit goes hand-in- hand with the provision for adequate ventilation.
As a result, we must surely consider air management as a fundamentally important factor in the delivery of a safe and functional home.
Mechanical ventilation systems may need servicing and maintenance, while passive vents servicing sub floor and roof voids must be kept clear and unobstructed. The implications of poorly-installed, unserviced and inappropriate ventilation systems include the perpetuation of damp living conditions, however in some circumstances defects in ventilation can be a threat to life.
On a learning curve
In summary, as retrofit insulation becomes more common and ventilation more critical, the building sector will face an increasingly complex and challenging environment.
In changing times, it is critical that the industry advances its knowledge to deal with this new situation.
A starting point for this is the PCA’s 2019 International Building Preservation Conference, which takes place on 21st November at The Slate, University of Warwick.
The event will focus on topics relevant to all those involved in the preservation sector.
More details can be found at https://www.property-care.org/conferences/building-preservation-2019/
- Log in to post comments