The recent statement by Secretary of State for Housing Robert Jenrick, announcing the 2021-2026 £11.5bn Affordable Housing Programme, sets out a series of ambitious housebuilding targets to help improve the efficiency of the UK development sector.
Organisations seeking Grant and looking to sign “strategic partnership” deals with Homes England to build large numbers of affordable homes will have to commit to using modern methods of construction (MMC) to build at least 25% of their pipeline.
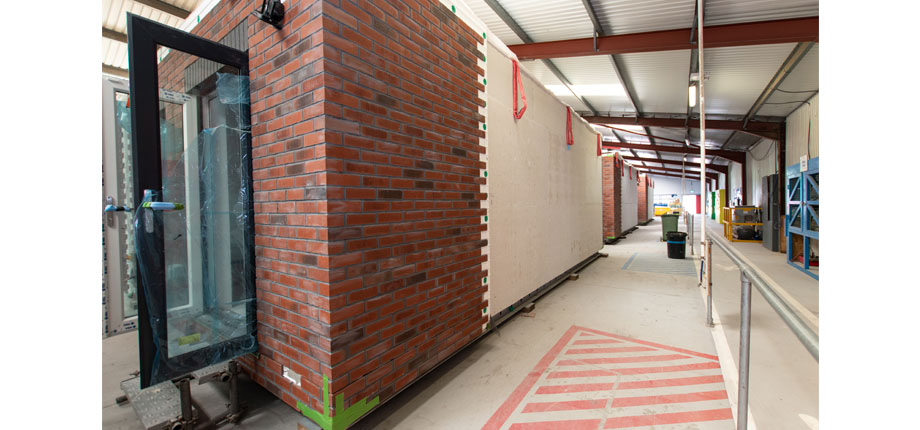
Despite recent events that have steered the housing agenda away from the top of the Government list of priorities, the requirement for more affordable housing is as important as ever. Last year there was a national shortfall of more than 800,000 homes across the UK which is not predicted to be any less severe in 2020/21.
Social landlords need to adapt their programmes now to meet the new requirements. This however should not be seen as another bump in the road, but rather an opportunity to finally build more sustainable, affordable, decent homes. The traditional approach to development is simply outdated and not fit to deliver such targets. Factory built homes are quicker to produce, to a higher quality, generate less carbon (in construction and in use) and can be more cost effective to maintain.
The coronavirus outbreak stalled many development programmes. This in turn will create further increased demand and a requirement to produce more cost-effective homes, faster, when the dust settles and the construction sector is able to return to normal.
Offsite manufacture has been available for a long time, but unlike other sectors housing has been resistant to change. We all agree the concept is sound, but most affordable housing developers then find good reasons to do it the way they always have. Now it is finally time to start incorporating MMC in their programmes at scale.
THE CHANGE STARTS WITH EFFECTIVE PROCUREMENT SOLUTIONS
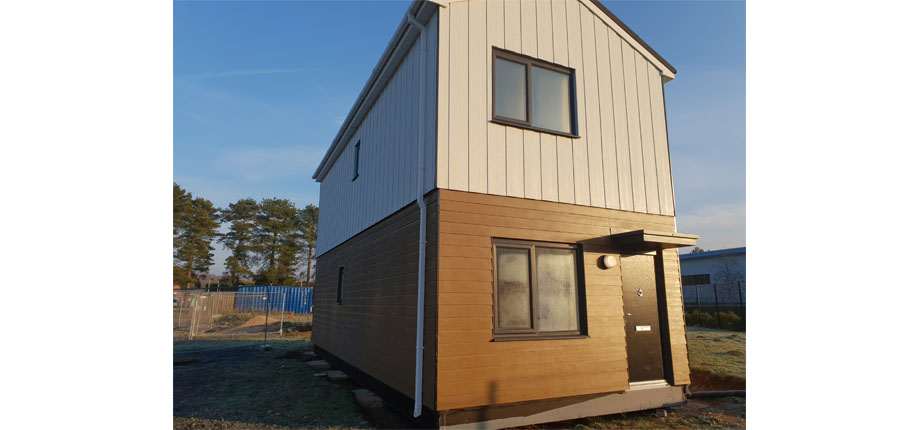
So, where do we start? To deliver a successful MMC development programme, support from trusted experts and an efficient route to market are key. With the affordable housing sector being slow to embrace the change to modular, many procurement providers do not yet have a tried and tested solution in place; but the Central Housing Investment Consortium (CHIC) has just that.
Changing the face of housing delivery through MMC, particularly full off-site manufacture, has been on CHIC’s agenda for many years, being amongst the few early adopters to deliver a procured solution.
CHIC’s modular BuildSmart services were first procured in 2015. Being a housing consortium provides a unique perspective to gain insight into the direction of the UK housing market. Having a close relationship with both housing and construction professionals means that CHIC can develop long-term contracts that accommodate the needs of a changing market.
CHIC has now procured 3 new long-term contracts; each is for an initial period of 5 years, extendable for two further periods of 5 years.
All 3 contracts provide for the offsite manufacture (factory build) of new homes, plus on-site erection, and completion. However, uniquely, all manufacturers are also main contractors, offering a full turnkey solution where required.
CHIC has developed a range of standard house types. The contracts can us these or alternatives and cover options for houses and low rise flats, as well as more dense medium and high-rise apartments.
All solutions are available to local authorities and housing associations across England, Wales and Scotland, who need not only a compliant procurement ‘route to market’ but also a tried and tested solution.
“CHIC has been actively promoting offsite manufacture for many years and this new suite of turnkey contracts provides a great solution for our members and prospective members to embrace modular construction. We look forward to supporting the efficient development of new housing with our partners” says John Fisher, Managing Director of CHIC
Visit the CHIC website here
- Log in to post comments