Fire safety is critical but ensuring that an EWI system has been tested for windloading capabilities shouldn’t be overlooked. Mark Weaver, Alsecco’s Regional Manager explains...
When specifying materials for use on high-rise buildings, whether as the overclad of an uninsulated residential block or replacing unsuitable existing cladding, there are key aspects to consider. As well as the materials chosen, the choice of system designer and installer are equally crucial in being able to tackle these specialist building types.
External Wall Insulation (EWI) is a technology employing insulation boards to masonry walls in a refurbishment setting, or to the sheathing layer of new build schemes with steel framing or concrete frame with SFS infill. Alsecco has been a leading supplier of External Wall Insulation for over 25 years in the UK and is the UK operation of the international DAW Group, innovators in EWI since 1957. Alsecco’s founder in the UK in 1995 was an engineer with the utmost focus upon safety, best practice, testing and brand reputation and these principles remain embedded within the company’s DNA. If you are considering an EWI supplier, look no further than Alsecco with their detailed attention to fire safety, windloading resistance and technical project management.
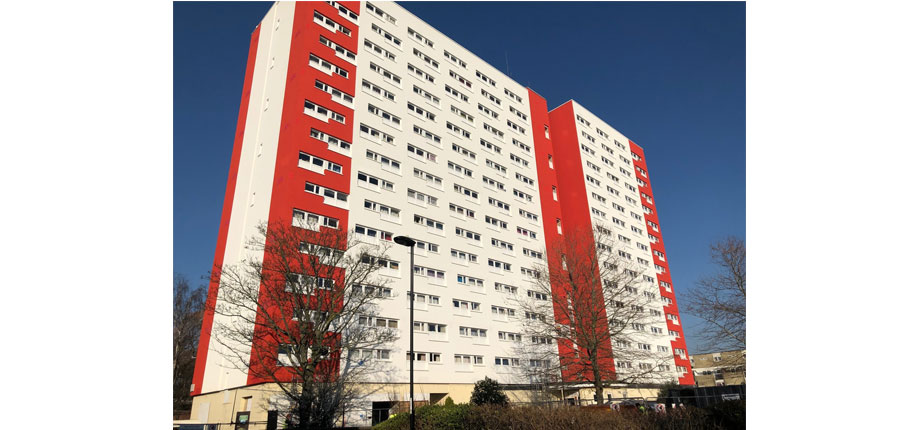
Above: When Albion Towers, close to Southampton’s St Mary’s football ground, were being renovated with Alsecco’s system, choosing the colours was an easy decision!
FIRE SAFETY
Tenant and resident safety has always been at the very top of Alsecco’s considerations for its EWI systems so the latest changes in regulations over 18 metres has made no difference to Alsecco’s specification policy. All buildings with an EPS (polystyrene-based) system over two storeys will have mineral wool firebreaks specified at each floor above the second level and Building Regulations allow this at present up to 18 metres for England, Wales and NI, 11 metres for Scotland. As the number of storeys over two increases though it is often recommended by Alsecco to use the Ecomin mineral wool based system as once fire breaks are introduced to an EPS system above two storeys, it is often more cost effective to cover the entire building in the Ecomin system. As the storeys increase above the first floor, this decision becomes more clear-cut with cost benefits, simplified design, installation and supervision. As the Ecomin EWI system is fixed directly to either the masonry substrate or sheathing board for framed areas, without the requirement of a cavity, then the overall design and construction is extremely simple to carry out and supervise as the complete façade is A2-s1, d0 Euroclass fire classified. Alsecco are also mindful that fire services tackling, for instance, a fire that is breaking through a high level apartment window have a better understanding of how a fire behaves in relation to the façade if all floors are of a consistent material and design. Fires in apartments have not been uncommon over the 25 years that Alsecco have been supplying EWI systems to high rise and the Ecomin system generally requires no more than system repair around the perimeters of the affected window area, another significant advantage of a system of limited combustibility. Alsecco’s technical support for every scheme it supplies will include all installation guidance to cover all aspects of fire safety including the relevant supplementary fire fixings, and all parties can be confident in the guidance provided for every project in which Alsecco are involved.
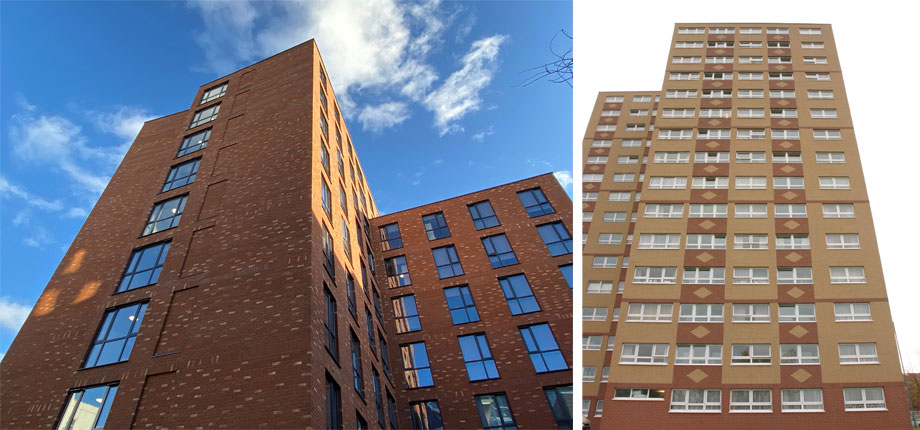
Above Left: There is no height limit to the use of Alsecco’s Ecomin clay or lightweight brick slip systems as both are Euroclass A2-s1, d0 fire rated.
Above Right: Although refurbished with Alsecco’s Meldorfer lightweight brick slips over twenty years ago, the appearance of these blocks in Bristol remains as good as new
WINDLOADING PERFORMANCE
There has understandably been tremendous focus recently upon fire safety, but of huge importance is also the resistance of a cladding system to the significant wind forces exerted upon a building. How can a specifier or client be assured that the system employed is able to withstand these forces? In this respect, Alsecco has data to hand to provide this assurance.
Alsecco’s most recent iterations of their BBA Certificates contain reassuringly robust paragraphs, specifically section 7.13 in certificates for both Ecomin systems, Ecomin 300 for a render finish and Ecomin 400 for a brick finish. The section centres upon the Dynamic Wind Uplift (DWU) test carried out on Alsecco’s Ecomin mineral wool system. Put simply, a DWU test is a wind chamber test designed to ‘suck’ materials from the test rig, replicating extreme wind conditions.
The Ecomin system recorded a result of 4.95 kN/m2 (in fact, this was the highest measure that the chamber could exert before being switched off, with no materials damaged in the test) and the stated value in the BBA Certificate shows 3.33 kN/m2 when reduced by the BBA safety factor of 1.5. Crucially, without this result specific to the system tested, and included within the BBA Certificate, the default wind resistance of a mineral wool system for a BBA Certified system is 1.1 kN/m2, insufficient to provide complete confidence for high rise or exposed buildings. This default value is determined by the BBA as the weakest interface of an EWI system since, in lieu of a verified DWU test, they have no evidence on which to determine a system’s capabilities to resist wind loads.
This industry-leading wind performance is testament to Alsecco’s highest quality mortars, brought about by years of DAW product development, and innovative adhesive and mechanical fixing methodology and can be written into performance standards to ensure that system design exceeds building-specific wind conditions. Repairing a facade damaged by adverse wind forces is not an attractive proposition.
Alsecco undertake a project-specific system specification for every scheme it supplies meaning that prior to any materials being installed, experienced technicians will carry out substrate pull-out tests, u-value calculations, condensation risk analyses and windloading calculations. From this information Alsecco determines the exact mechanical fixings type required and the pattern of fixing including all required fire fixings. As installation progresses, technicians make regular site visits to ensure that the installation meets the specification and practices of good installation.
BRICK FINISHES
So it is clear that when specifying the most suitable system for safe high rise cladding, Alsecco has all of the necessary credentials to meet the needs of clients, insurers and residents. And when the most desirable finish to a façade is expected, Alsecco can provide a wide range of decorative, low maintenance finishes. The highest quality silicone render top coat finishes are provided through the extensive R&D and innovation of the DAW Group, and if a brick finish is required then Alsecco has an offer that includes both purpose-made clay, ceramic or stone appearance slips or lightweight Meldorfer flat-facing slips for a more economical solution to providing a brick-effect appearance. Suitable for use over 18 metres with A2-s1, d0 fire classifications, both systems utilize Alsecco’s specialist mortars, purposely designed for each element of the system build-up. Extensively used on new build schemes where construction requires high thermal performance alongside speed of construction and simplicity of design, brick slip systems are a perfect solution for cladding sometimes drab high rise residential blocks with attractive combinations of brick and render combined. Alsecco offer a popular brick matching service so if a specific brick appearance is required to meet planning requirements, it can be found with clay or Meldorfer lightweight alternatives. These low maintenance solutions can retain the traditional appearance of masonry but with a highly thermally efficient system to retain warmth within the building and minimize energy bills.
The renovation of large residential buildings is under such close scrutiny for all of the right reasons, so it is incumbent upon designers, landlords and contractors to ensure that the systems that they employ to thermally and decoratively clad these buildings meet all aspects of safety and security, and with Alsecco there is the confidence of working with a safe, knowledgeable and experienced supplier.
Visit the Alsecco website
Email: sales@alsecco.co.uk
- Log in to post comments