Housing associations have a pivotal part to play in supporting the UK’s journey to net-zero but further change is needed if we’re going to get there.
The UK has some of the most energy leaking housing in Europe, much of it built in the pre-war period.
According to the National Housing Federation the UK’s 29million homes produce 58.5million tonnes of CO2 every year. That’s more than the CO2 produced annually by all car journeys.
It also makes up round 14% of the UK’s emissions and with a commitment to cut total UK emissions by 80% relative to 1990 levels by 2050 under the Climate Change Act (2008), that’s a big problem for Government.
With around 2.7million homes across England, on their books, housing association owned and managed properties account for one of the single biggest ‘slice’ of emissions, creating an opportunity for big wins in the fight against climate change.
“Get the road map right for carbon reduction in housing association-owned properties, and the UK can take a big step forward in reducing CO2 emissions from homes in a single sweep”, explains John Duckworth, Director of Commercial Sales, Deceuninck (pictured left).
“A more effective approach to the building fabric has the potential to significantly lower energy consumption in new and existing properties through retrofit.
“The challenge is that right now, that road map isn’t entirely clear, and funding remains, and is likely to remain, a pressure point, so housing associations and their supply partners need to innovate to get where it’s universally agreed, that we need to go.”
To get across the 2050 carbon neutral finishing line, those 2.7million homes will need to achieve an Energy Performance Certificate C rating or above.
This at present appears some way off, with more than 60% of social properties in England and 44% of social homes in Wales, falling below the EPC standard.
New build social homes fair better, but top A-rated properties still only account for fewer than 1.2% - just 607 – of the 50,000 new social housing properties completed in the UK last year.
“The Government has pledged £3.8bn to the Social Housing Decarbonisation Fund, to try and address the deficit in energy performance in existing properties through retrofit.
“It’s also said in the autumn statement that it would make a further £6billion of new funding available from 2025 to 2028 for energy efficiency.
“It isn’t, however, only about funding - but also strategy. How can a more effective approach to the building fabric be developed to meet the UK’s climate change ambitions, both in terms of retrofit – but also new build social housing.”
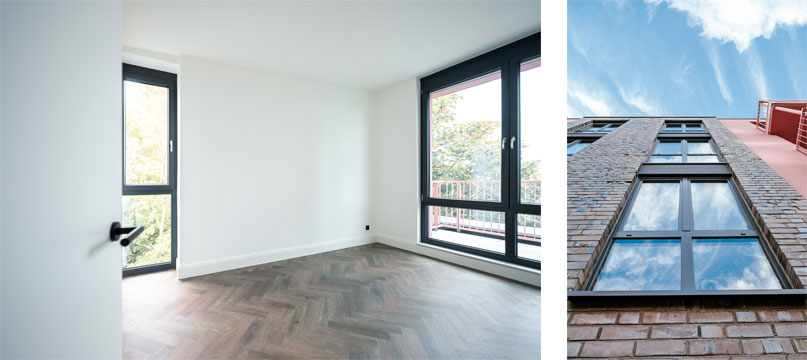
Images © Deceuninck / mfh-osterstrasse
The impact on window and door specification
As a key element of the building envelope and a potential major source of CO2 (according to Government figures, 18% of heat loss occurs through windows), windows and doors are a key element of the building fabric.
This was recognized in the changes to Part L that we saw last year which introduced a new requirement of 1.2W/m2K for new build windows and doors with a glazed area of more than 60%; and 1.4W/m2K for replacement windows and doors.
“The changes that we saw last year, are in fact just the start of what will be a series of performance changes for windows and doors in the coming two-to three years, with consultation on future changes to Part L, and under the Future Homes Strategy, imminent”, continues John.
“This could see u-values for new build reduced to as low as 0.8W/m2K, or more likely 0.9W/m2K. Even at the latter, housing associations and their supply chains, are going to have to re-think window and door specification because products as they sit today, aren’t going to deliver required performance.”
Triple-glazing
U-values of 0.9W/m2 K immediately push window and door specifications into triple-glazing but John argues that the ramifications are broader.
“A lot of older aluminium systems are simply going to fall short but even for far more thermally efficient PVC-U options, there are also challenges”, John says.
“That’s why Deceuninck is developing a new generation of products which use less carbon in manufacture but which also deliver higher levels of thermal efficiency and reduce carbon, through life.”
Elegant - next generation window performance
This includes Elegant, Deceuninck’s new energy efficient fiberglass composite window system redefines expectations of performance including U-values as low as 0.8W/m2K. This goes far beyond current building regulations, future proofing its offer to the specification sector.
It’s defined by contemporary minimalist features, creating a strong architectural aesthetic which replicates aluminium in an advanced, low maintenance and energy efficient, composite system.
John continues: “Elegant, our award winning, new ultra-energy-efficient window and door offer sits within our wider sustainability strategy.
“It’s a next generation window system which has been designed to deliver exceptional through life performance, while also being designed to be easier and use less energy to recycle at end-of-life”, he explains.
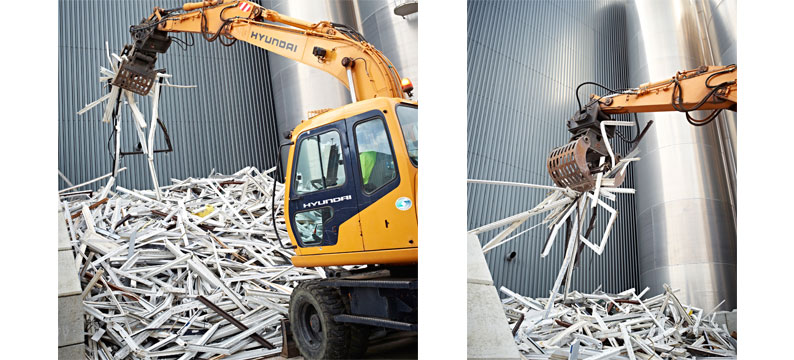
Image © Deceuninck
Working to in partnership to support housing associations to lower their carbon footprint.
This focus on sustainability continues through to Deceuninck’s commitment to ambitious targets to reduce greenhouse emissions through the corporate carbon reduction scheme, Science Based Targets (SBTi).
This includes a commitment to cut the CO2 emissions from its own operations (Scope 1&2) by 60% by 2030 from a 2021 baseline. Allowing for future growth in real terms this means reducing CO2 per tonne of product produced by 75%. This goes significantly beyond the SBTi minimum target of 42%.
It has also committed to cut emissions from within its supply chain (Scope 3 emissions) by 48% per tonne by 2030, as part of its wider journey to net-zero greenhouse gas emissions by 2050.
As part of this strategy Deceuninck has invested more than €15million in one of the world’s most advanced recycling and compounding facilities to create the capacity to reprocess up to 45,000 tonnes of post-consumer and post-manufacturing PVC-U per year.
In real terms this gives it the capacity to prevent more than three million windows from going to landfill annually.
“The window and door industry is committed to rising to the challenge. Deceuninck for one, is committed to developing low carbon manufacturing technologies and a new generation of products which deliver big through-life energy efficiency gains”, John explains.
“Big changes, do however, need to be made if we’re going to get to net zero. That’s going to require a re-think about the way in which new build and replacement windows are specified by housing associations and main contractors.”
For more information about Deceuninck’s product and service offer please call 01249 816 969, email deceuninck.ltd@deceuninck.com or visit www.deceuninck.co.uk
- Log in to post comments