Changes to Part L have significant ramifications for new build – but also replacement programmes. We report...
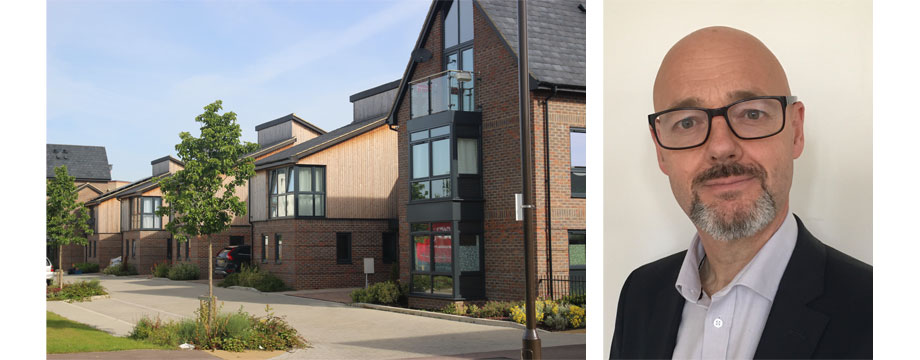
The Government is expected to unveil its interim update to Part L next month [Oct]. Stopping short of the far more comprehensive changes to follow in 2025, with the introduction of the Future Homes Standard, they nonetheless have significant ramifications for new build and refurbishment programmes – including windows and doors.
John Duckworth, Head of Sales, Commercial, Deceuninck, explains: “The Ministry of Housing Communities and Local Government (MHCLG) is expected to publish its revision of Part L in this October, coming into effect in England and Wales from July next year.
“While it doesn’t go anywhere near as far as the Future Homes Standard, its ramifications are significant for new build and refurbishment projects, pushing up minimum standards at a time when COVID-related supply chain disruption is already pushing up costs and disrupting delivery.
“Planning now to take out the guess work is critical.”
What are the changes to Part L?
The current round of changes to Part L need to be seen within the Government’s broader strategy to decarbonise UK homes set out in the Future Homes Standard. This sets out new requirements to make all new homes ‘zero carbon ready’ by 2025, reducing carbon emissions by a minimum, 75% compared to present.
New homes will also have to be future-proofed, so there will be no requirement for future retro-fit work and there will be a ban on the installation of new heating systems which use fossil fuels, for example gas boilers.
Existing homes will also be subject to higher standards – with a ‘significant improvement’ on the standard for extensions, making homes warmer and reducing bills. Replacements and repairs will also have to be more energy efficient. This includes the replacement of windows and doors as ‘controlled fittings’ under building regulations.
As a point in the journey to the Future Homes Standard, the current revisions of Part L are aimed at achieving a 31% reduction in new home carbon emissions from next year.
“Although nothing is hard and fast, the changes to Part L (Conservation of Fuel and Power), which will be mirrored by corresponding changes to Part F (Ventilation) to prevent over-heating of homes, will focus on a fabric first approach”, continues John.
“This is aimed at reducing the energy used in keeping homes warm, and ventilated, by upping the specification of the building envelope.
“For windows and doors, that’s expected to include an upping of the minimum requirements for replacement windows from 1.6W/m2K to 1.4W/m2K;
and doors from 1.8W/m2K to 1.4W/m2K. In newbuild, u-values are expected to be dropped to 1.2W/m2K.”
Implications for window and door specification
Although he emphasises that until published, regulations remain subject to potential change, John argues that the direction of travel is clear, pushing window and door specification towards higher levels of performance, something which he warns less energy efficient systems will struggle to meet.
“If newbuild window and door specifications move to 1.2W/m2K as the consultation document suggests then the only way some window systems will get there is by upping specification to triple-glazed units, or very high performing double-glazed units”, he argues.
“That carries a cost and budgetary implication for projects started after the cut-off point at a time when delivery costs are already higher.”
He warns that given the length of time it takes for new build projects to break ground, it’s important that housing association providers pursuing new build programmes plan ahead, to understand where their projects fall in relation to the cut-off point.
Where plans are submitted this side of July 2022, it is expected that they will need to break ground by June 2023 to fall under the ‘old’ 2013 Part L requirements. Those where notices are submitted after June 2022, or which aren’t started until after June 2023, will fall under the new regulations.
“I suppose you could argue there is an advantage in moving projects forward – at least from a cost perspective, although, that’s not necessarily in the spirit of what of what the Government is trying to achieve here, and ultimately climate change is going to affect all of us.
“It’s better to focus on revising specifications through effective partnering, working towards those higher specifications - now. This allows you to improve through-life performance and to lower end-user energy consumption and costs, as well as plan effectively for the future”, John argues.
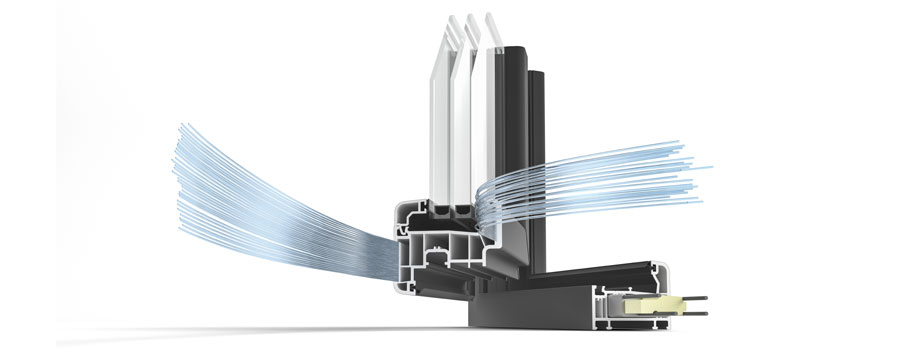
Future-proof
John argues that leading systems companies will have ‘tricks up their sleeve’ which will allow housing providers to meet higher specifications for new build window and door, as well as refurbishment programmes, without necessarily defaulting to more expensive triple-glazed units.
“Triple glazing will deliver a big uplift in performance but in resorting to a third more glass, you’re by definition increasing your costs, so you need to consider if it’s really necessary and if the uplift is justified in the context of lower cost upgrades to other elements of the building envelope”, John explains.
As specialist partner to the specification sector, Deceuninck’s own product offer is built around a range of flexible designs – each delivering maximum thermal performance.
This includes:
• Traditional 2500 Series – deliver a clean minimalist design, achieving u-values as low as 0.91W/m2k
• Heritage 2800 Series – sculptured design replicates the elegance of traditional timber with the efficiency gains of PVC-U including u-values as low as 0.91W/m2k.
• Contemporary 5000 Series – Deceuninck flagship commercial system the 5000 series to extend the design potential of PVC-U using patented glass fibre technology, removing the requirement for steel reinforcement, increasing thermal efficiency with u-values as low as 0.76W/m2k while reducing weight.
• Fully Reversible Window - Designed for medium to high rise developments it achieves u-values as low as 0.96W/m2k.
John highlights Deceuninck’s 5000 composite system, as offering specific efficiency gains. It uses Deceuninck’s patented Linktrusion technology to combines the strength and looks typically associated with aluminium with the superior energy efficiency performance of PVC-U.
Particularly well suited for commercial projects, it’s been designed to allows developers to specify outsized windows and doors with slim-sightlines, without the need for traditional steel reinforcement.
Offering up 30% improvement in thermal efficiency, 40% savings on materials and weight, it delivers U-values as low as 0.76W/m2k with argon filled triple glazing.
“Some of those u-values we’re quoting are achieved using a triple-glazed unit but you will still be comfortably able to accommodate expected new replacement and new build requirements under Part L with a double-glazed unit”, John says.
“You don’t have to default to a triple-glazed unit to meet expected changes to Part L requirements but you do need the right system and system partner.
“As we move towards the Future Homes Standard, now not so very far away, that may change but even with the more stringent requirements we expect to see by 2025, leading window and door systems already have the technologies in place to meet them and we and others, are working on future innovations to do that even more efficiently.”
Call 01249 816 969 or visit the website for more about Deceuninck’s commercial range and commercial work. You can also download Deceuninck’s full product portfolio from the NBS National BIM Library
- Log in to post comments